Under Pressure Solutions
ECAL/Ecole Cantonale d'Art de Lausanne (HES-SO)
In a rapidly changing world, industrial design is facing new challenges. For the 2024 Milano Design Week, ECAL presents UPS – Under Pressure Solutions, an experimental research project aimed at reducing the environmental impact of the furniture industry through the use of shape memory materials.
The exhibition shows the process and results of this exploration led by five industrial designers teaching at ECAL, as well as objects designed by Master Product Design students, revealing the innovative and creative potential of cellulose sponge.
Milano Design Week 2024
16–20.04, 11am–8pm
21.04, 11am–4pm
Spazio Orso 16
Via dell'Orso 16
20121 Milano
We live in a digital era. Nowadays, every object in our daily life can be ordered online and delivered to our home
Take furniture. In order to minimise the environmental and climatic impact of buying furniture, two elements are essential: optimising transportation or relocalising the production. These constraints bring new technical and aesthetic challenges to the field of industrial design.
The idea of locally sourcing furniture production was one of the ideas explored in ECAL’s Digital Market, which was a new design production platform presented in 2018 during the Milan furniture fair. As part of the presentation, Master Product Design students created a range of everyday objects, which were then produced by a print farm located within the exhibition. The objects were sold directly on site, transforming the furniture store into something that works much more like a bakery.
UPS – Under Pressure Solutions – offers a new approach to solving the transportation issue. In this case, by imagining a lightweight furniture system made of cellulose sponge – a biosourced and biodegradable material. The objects can be shipped in a compressed form. Once they have reached their destination, they are moistened, allowing them to expand and reconfigure themselves – no mechanical assembly needed.
The idea of optimising the packing of industrially-produced furniture is not new, particularly when it comes to seating elements. The concept can be traced back to the Austrian cabinetmaker Michael Thonet. His famous No.14 Chair was created in 1859 using a then-new bentwood technique. It could be mass-produced in parts, thus enabling 36 disassembled chairs to be stored in one cubic meter. Pushing the idea further, Gerrit Rietveld’s 1934 Crate Chair was designed using leftover material from wooden crates used for shipping other objects, and was conceived of as a kit for self-assembly. Those ideas led to innumerable variations on the ideas of home assembly and flat-packing.
In 1969 in Milan, Gaetano Pesce imagined a different approach. His iconic UP5 armchair was vacuum-packed to reduce it to one tenth of its final volume. Once the package opened, the chair inflated by itself, taking on its definitive form over the course of a few minutes. This spectacular unwrapping was presented not only as a technical process, but as an artistic happening – an integral part of the owner’s experience. It was made possible by the expansion of a polyurethane foam containing Freon, a gas that was later discovered to be harmful to the ozone layer. In consequence, despite its success and visibility, the product was withdrawn as early as 1979. A new version of the chair, without the expansion experience, was later commercialised.
The scene of a lifelike, self-forming UP5 armchair, also known as La Mamma or Big Mama, sparked the imagination of ECAL’s Master Product Design department. It eventually led to a two-year, in-depth research project investigating compressible materials, and what they could bring to furniture design.


Chris Kabel


Chris Kabel


Chris Kabel
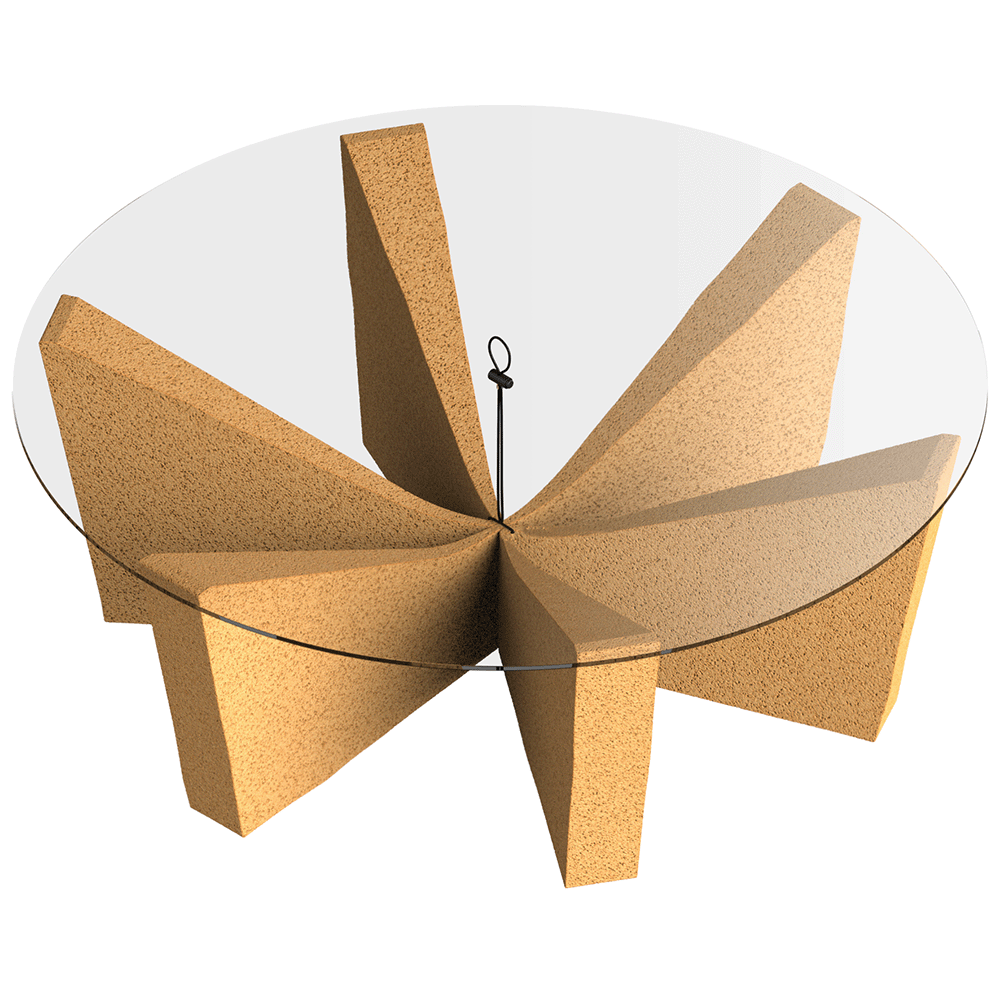

Anthony Guex
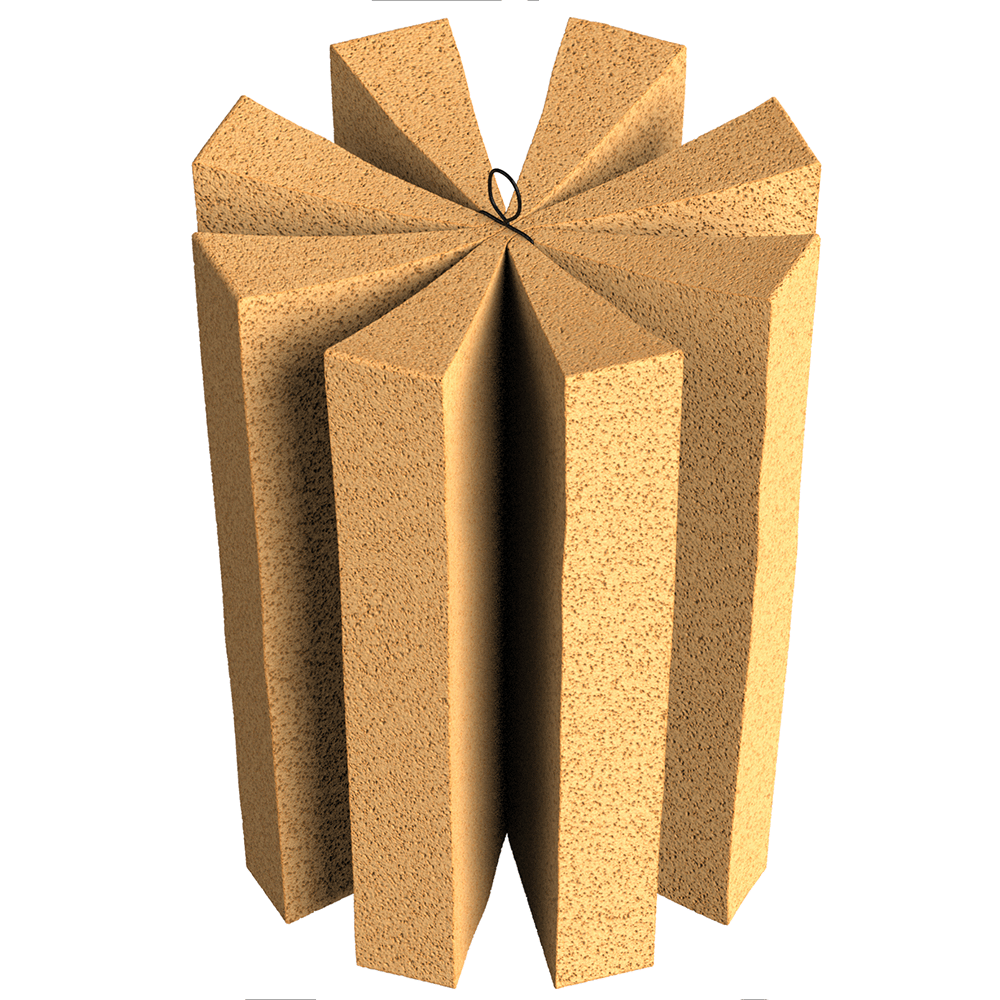

Anthony Guex


Anthony Guex

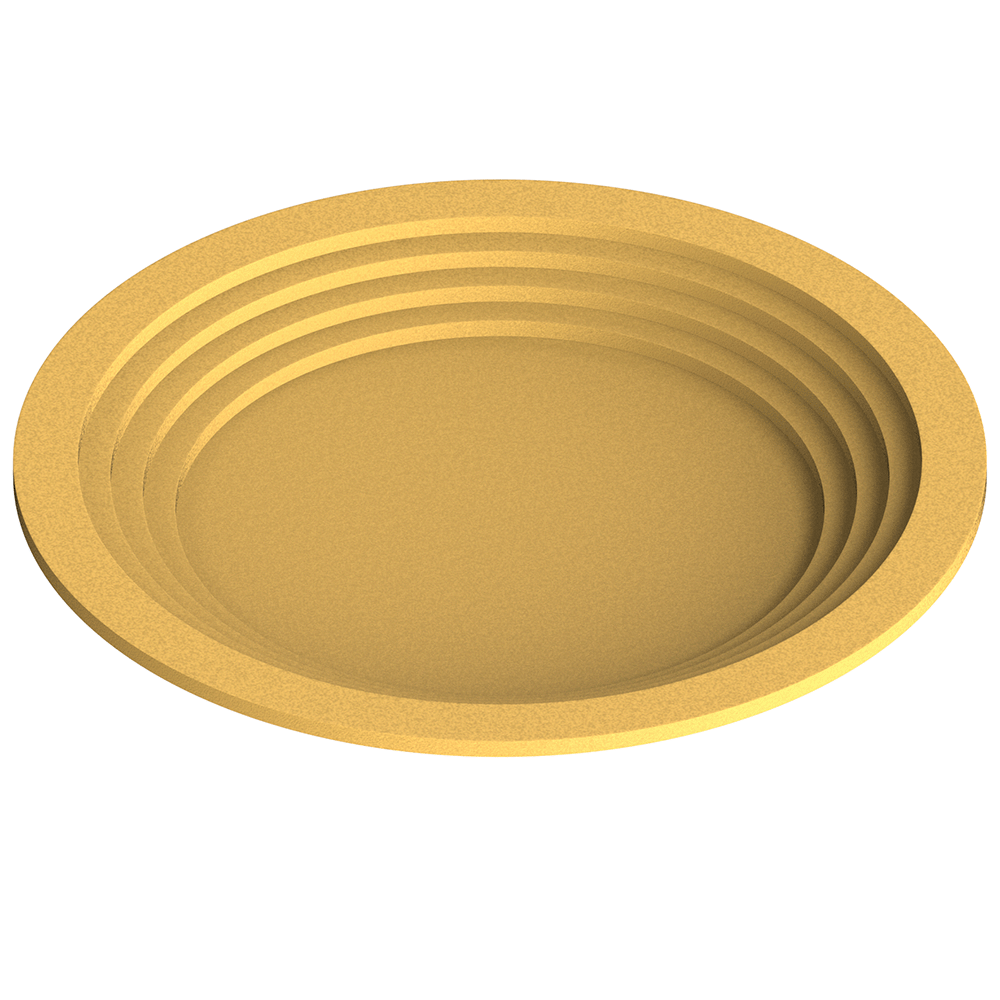
Christophe Guberan

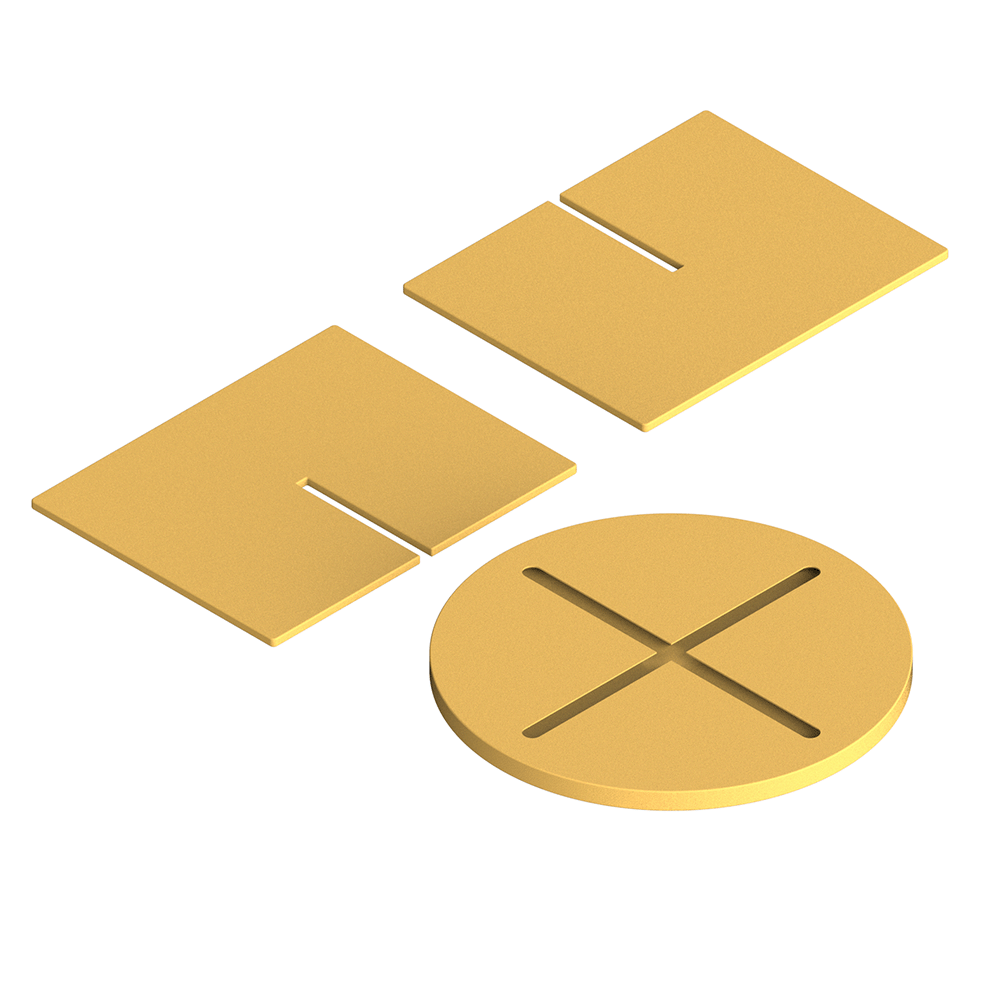
Christophe Guberan

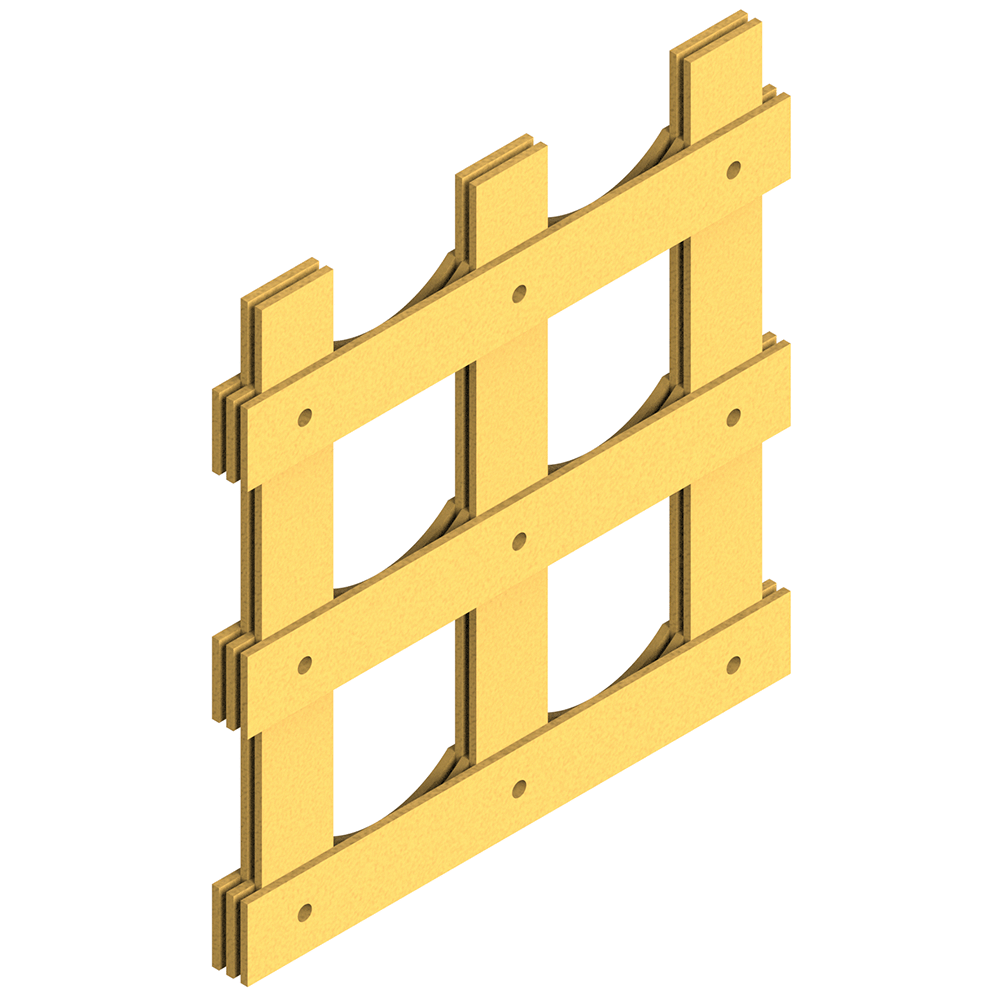
Julie Richoz

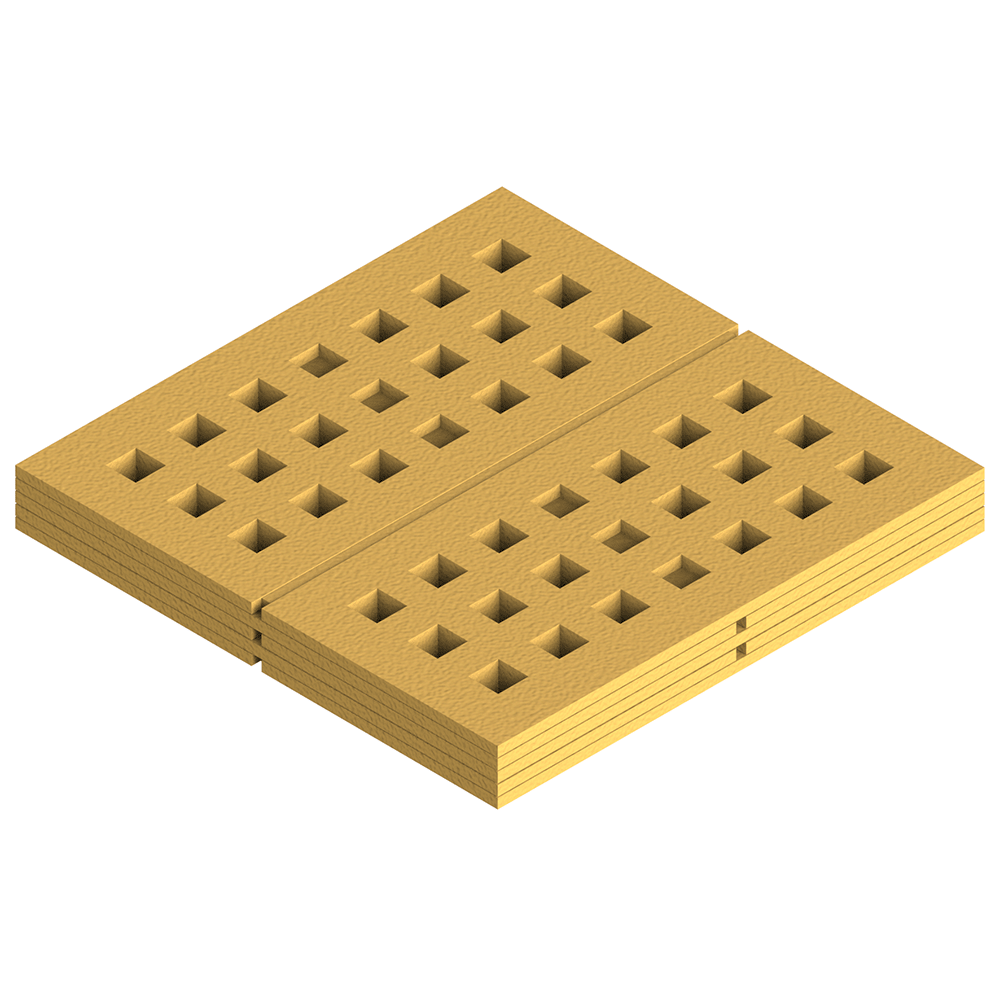
Camille Blin


Camille Blin

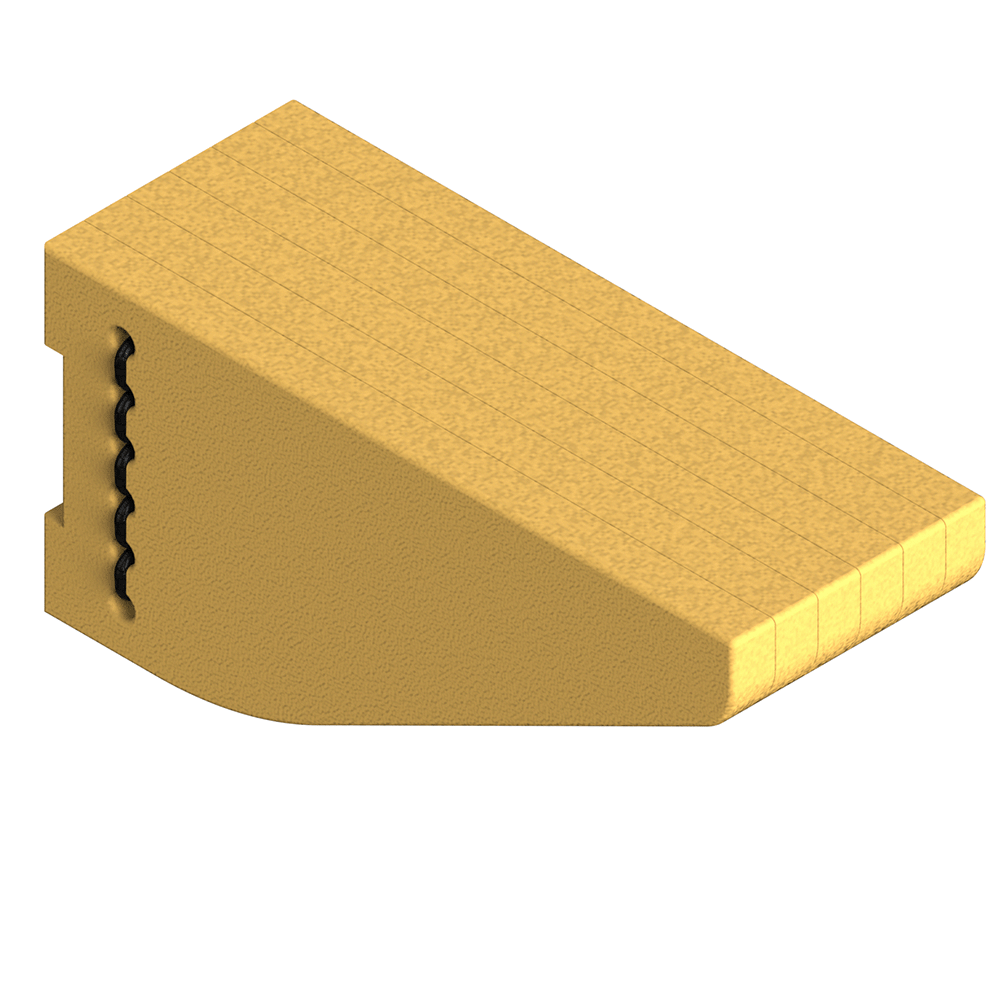
Clémentine Merhebi


David Ortiz Quintero

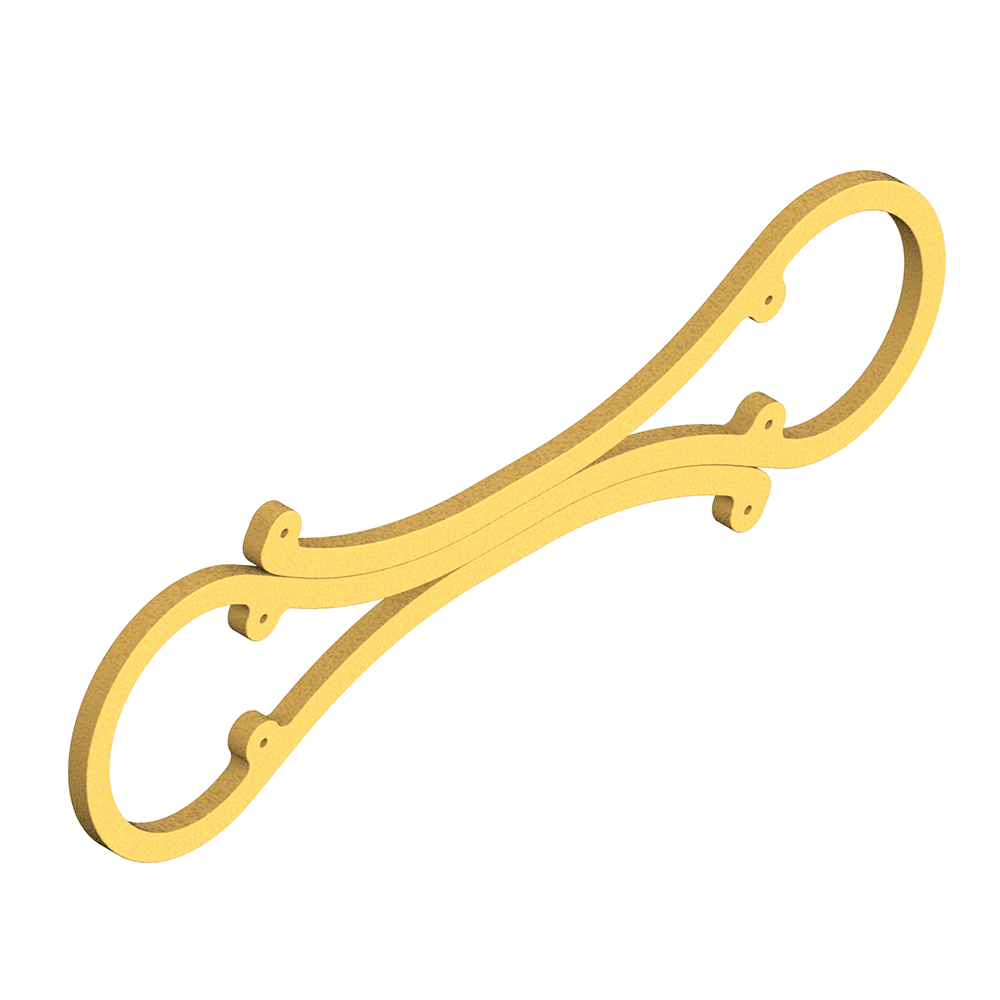
Brice Tempier

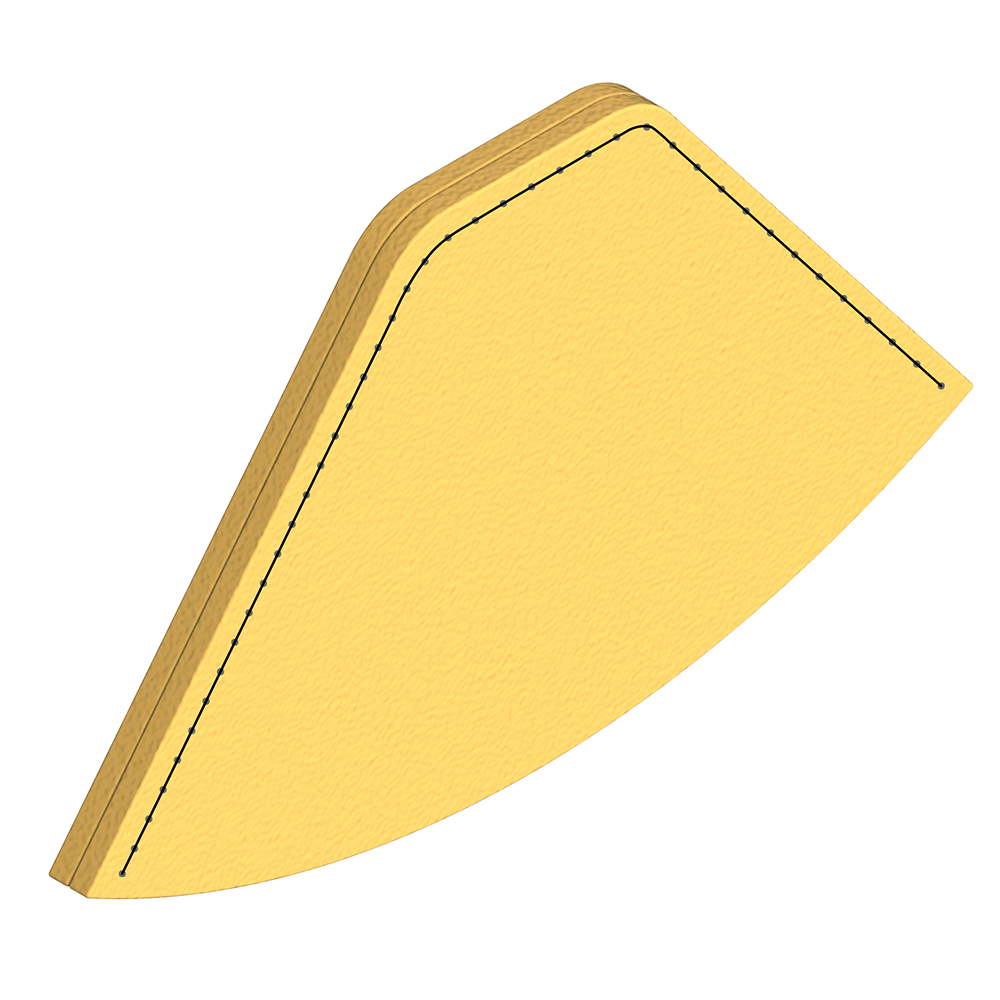
Louis Bosnjak

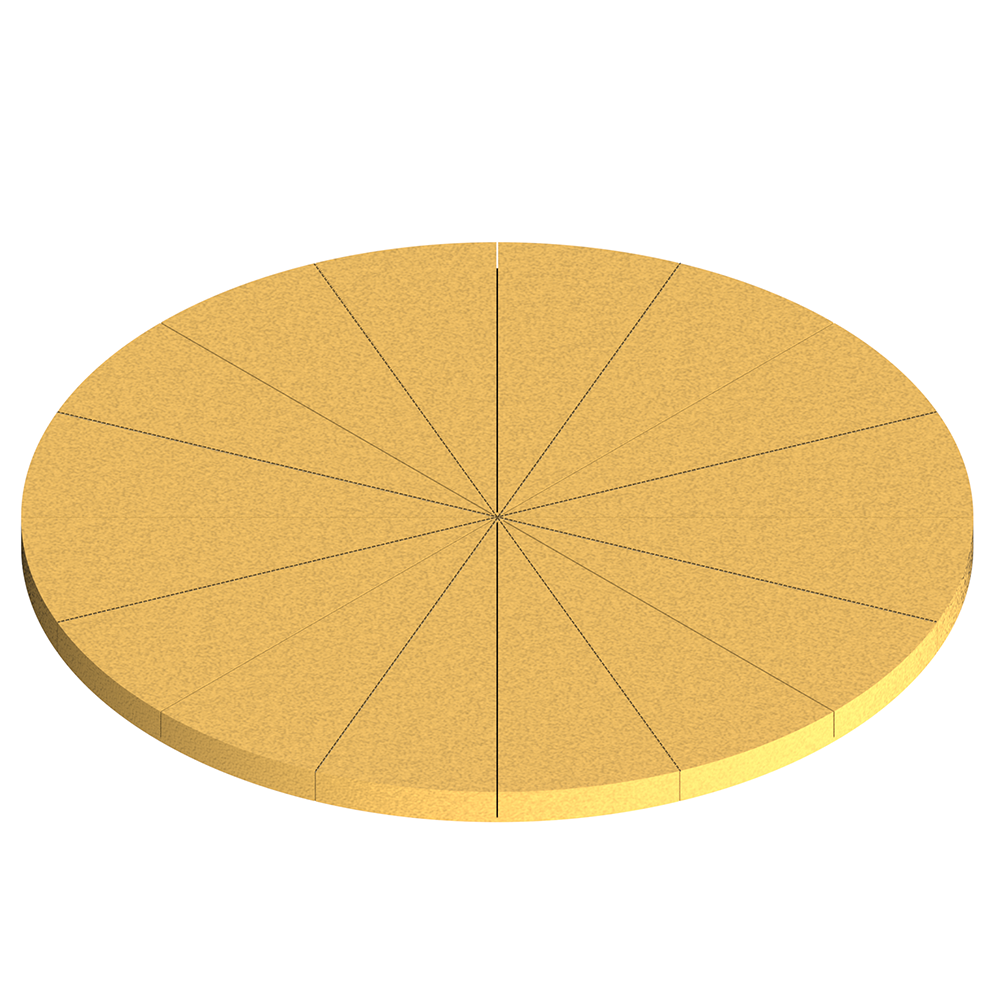
Marco Ciacci
Second Prototypes
March 2023
These are the final results of the experimentation with cellulose sponge. After having tried to create complex seating solutions, such as chairs with back elements, each of the five participating designers came up with a final prototype for a basic stool. The proposed stools offer variations on the principles of cutting and stacking dried sponge plates.
First Prototypes
February 2023
Each of the five participating designers proposed an advanced prototype of a cellulose sponge seating element. Based on the previous experimenting and testing phases, they all decided to work on variation in stacking possibilities of different sponge plates.
Experiments #3
Cellulose sponge, November 2022
During two 3 days workshops, the five participating designers (Camille Blin, Christophe Guberan, Anthony Guex, Chris Kabel and Julie Richoz) tried to create a viable proposition for a compressible cellulose sponge seat.
The following scenario was envisioned: a user receives a compressed dried plate. He then moistens it, the object expands into its final shape, and then must be left to dry before finally being ready for use as a seat. With this scenario in mind, the designers worked collectively on different ideas to create prototypes that would present the following qualities: an efficient production process, a design that would facilitate the expansion and minimize the amount of water needed, as well as shortening the drying phase.
After a lot of experimenting, the most accessible and efficient process was deemed to be working with assembled dried sponge plates. Its striking efficiency was demonstrated by the very first basic cylindrical stool test in the previous phase.
Experiments #2
3 materials, October 2022
Contacts were established with manufacturers of the 3 materials selected during the first experimentation phase (Enkair, cork and cellular sponge). Larger quantities of the 3 materials were obtained for advanced testing and an evaluation of prototype production feasibility.
Experiments #1
10 materials, August 2022
The sketches were confronted to reality. Samples of the 10 materials and processes (cork, enkair, spacer fabric, cellulose sponge, granular jamming, latex and castor oil foam. paper, nitinol, auxetic 3D mechanism) that were selected during the previous phase were obtained. During a collaborative workshop, the five participating designers (Camille Blin, Christophe Guberan, Anthony Guex, Chris Kabel and Julie Richoz) were able to physically assess the materials’ qualities, and to test the concepts they had previously laid out. For each of the 10 materials, some specific mechanical properties were also investigated.
Based on the results of the workshop, the designers collectively selected 3 of those materials for more advanced testing and prototyping: cork, enkair and cellulose sponge.
Conceptualisation
20 materials, December 2021
Five established industrial designers, Camille Blin, Christophe Guberan, Anthony Guex, Chris Kabel and Julie Richoz were tasked with coming up with a concept, crafting at least one constructive idea in the form of a basic sketch for each of the 20 materials selected during the previous phase of the project.
Based on the sketches and discussions the 10 following materials were selected for the next phase, hands on experimentation: cork, enkair, spacer fabric, cellulose sponge, granular jamming, latex and castor oil foam. paper, nitinol, auxetic 3D mechanism.
Description
56 materials, September 2021
The 56 materials that came out as promising during the first phase needed to be more precisely documented. In order to get a better assessment of each of the material’s potential to ultimately be used to create compressible furniture, a cartography of their properties was established, as exhaustive as possible. An “ID card” was created for each material, consisting of an image, a general description, an in-depth description, and an evaluation with respect to the following criteria: compressibility, "sitability", accessibility, environmental impact. These qualities were empirically determined on a scale from 1 to 100 and subsequently represented on a spider diagram, offering a quick overview of these features.
This directory of "ID cards” was used to refine the selection, resulting in a set of 20 materials, deemed the most promising for further experimentation.
Prospection
150 materials, April 2021
The project’s first phase, aimed at prospecting materials with compressibility related properties. In a one week workshop, led by Anniina Koivu, Christophe Guberan, Camille Blin, the first year Master Product design students during the spring semester 2021 were asked to find as many of those materials as possible, and collect the available information on them. They assembled a catalog of more than 150 materials and mechanisms, ranging from well known natural and industrial products, to very advanced new processes, only developed in scientific labs. They were then tasked to evaluate them on three criterias: compressibility, organicity, and “sitability” (suitability to create a relatively confortable seat).
This evaluation and subsequent classification was done by empirically grading each material on three axes corresponding to the three investigated qualities. The result is a 3D cartography of the different materials and principles, giving an intuitive and rapid assessment of the relevance of their properties for the continuation of the research.
With help of this visual classification the matérials deemed too distant from the main goal (create a compressible piece of furniture) were removed, as well as those presenting too much similarity with one another or really too exotic to be realistically considered. The list was reduced to 56 materials, which were selected for the next phase.
Under Pressure Solutions
ECAL/Ecole Cantonale d'Art de Lausanne (HES-SO)
In a rapidly changing world, industrial design is facing new challenges. For the 2024 Milano Design Week, ECAL presents UPS – Under Pressure Solutions, an experimental research project aimed at reducing the environmental impact of the furniture industry through the use of shape memory materials.
The exhibition shows the process and results of this exploration led by five industrial designers teaching at ECAL, as well as objects designed by Master Product Design students, revealing the innovative and creative potential of cellulose sponge.